Introduction to Concentrated Solar Plants
Concentrated solar plants (CSP), is a type of solar power facility that utilises mirrors/lenses to focus sunlight to heat a fluent, e.g. special oil or molten salt, which subsequently is used to heat steam that drives a turbine/generator to produce electricity. CSP technologies have been demonstrated worldwide and recognised as low-carbon energy [1,2]. Next-generation CSP being developed in Europe [3] and the U.S. [4], c.f. Fig.1, aim to integrate ceramic particles as the primary heat transfer medium allowing thermal energy storage, with a secondary loop of supercritical carbon dioxide (s-CO2) utilising Brayton power cycles to operate between 700–1000 °C as to push the thermal efficiency boundary.
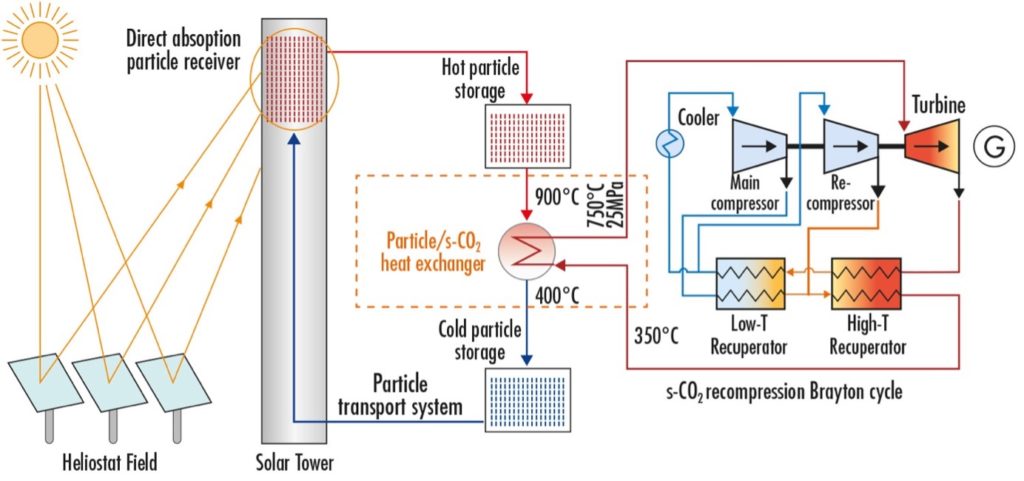
Figure 1
Material challenges in advanced CSP
However, this design poses considerable material challenges for the key components such as the heat exchanger tubes. These challenges include addressing issues such as strength, creep, erosion/wear resistance, particularly at temperatures exceeding 800 °C. Additionally, there is a need for resistance against oxidation on the outside surface and s-CO2 corrosion on the inside surface. Although the state-of-the-art commercial austenitic stainless steels, e.g. Sanicro 25 and P92, and nickel-based superalloys, e.g. H282 and IN740, manage to strike a satisfactory balance of properties within the temperature range of 600–750 °C, their suitability diminishes when exposed to temperatures surpassing 800 °C due to limitations in strength and corrosion resistance [5,6]. As a result, the quest for high-performance alloys based on refractory metals becomes imperative for the advancement of CSP applications.
Development of Cr-based alloys and innovation
Chromium (Cr) based materials are sought for CSP applications due to its high melting point (about 1900°C) compared with Ni. (1455 °C) and iron (1538 °C), low cost and good oxidation resistance. But the poor mechanical properties and brittleness at room temperature are their main drawbacks. Attempts have been made to improve the mechanical properties of Cr by conventional alloying approaches, but these issues still limit their application [7].
Inspired by the 𝛾-𝛾’ microstructure of face-centred cubic (fcc) Ni-based superalloys which exhibit an exceptional combination of strength, oxidation resistance and toughness, a new look to the design of Cr alloys has been taken. In our group, a prototype Cr-based ‘bcc-superalloys’ of the type Cr(Fe)-NiAl is developed, comprising a bcc-Cr(Fe) matrix (β) strengthened by ordered-bcc NiAl intermetallic precipitates (β’), with iron additions to tailor the precipitate volume fraction and mechanical properties at high temperatures [8], c.f. Fig.2. The Cr(Fe)-NiAl A2-B2 alloys show remarkably low coarsening rate at 800-1200 °C, outperforming ferritic-superalloys, cobalt- and nickel-based superalloys. The alloys show high compressive yield strength of ~320 MPa at 1000 °C. The Fe-modified alloy exhibits resistance to age softening, related to the low coarsening rate as well as the relatively stable Orowan strengthening as a function of precipitate radius. Microstructure tailoring with Fe additions offers a new design route to improve the balance of properties in Cr-superalloys, accelerating their development as a new class of high-temperature materials.
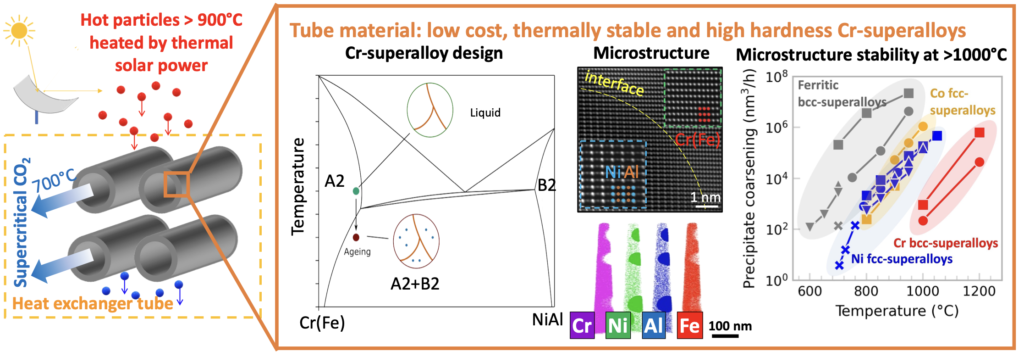
Figure 2
Further developments and research
More mechanical testing (small punch deformation/creep, 3-point bending etc.) and environmental experiments (oxidation, erosion, CO2 corrosion etc.) are ongoing. A high throughput method has been developed to investigate innovative Cr-based alloys, such as Cr-based high entropy alloys (HEA) and high entropy superalloys (HESA), in a larger compositional space.
People involved
Dr Kan Ma (research fellow), H2020 COMPASSCO2 funded.
Mr Thomas (Tom) Blackburn (PhD student 2021-2024), 2020 COMPASSCO2 funded.
References
[1] H. Müller-Steinhagen, F. Trieb, Ingenia 18 (2004) 43–50.
[2] S. Pfenninger, P. Gauché, J. Lilliestam, K. Damerau, F. Wagner, A. Patt, Nature Climate Change 4 (2014) 689–692.
[3] H2020 EU Project: COMPASsCO2 (https://www.compassco2.eu).
[4] Heliogen – First Quarter 2022 Presentation (Https://Heliogen.Com, 2022).
[5] M. Sarvghad, S.D. Maher, D. Collard, M. Tassan, G. Will, T.A. Steinberg, Energy Storage Materials 14 (2018) 179–198.
[6] J. Yin, Q. Zheng, Z. Peng, X. Zhang, International Journal of Energy Research 44 (2020) 1337–1369.
[7] Y. Gu, H. Harada, Y. Ro, Jom 56 (2004) 28–33.
[8] K. Ma, T. Blackburn, J.P. Magnussen, M. Kerbstadt, P.A. Ferreirós, T. Pinomaa, C. Hofer, D.G. Hopkinson, S.J. Day, P.A. Bagot, Acta Materialia (2023) 119183.